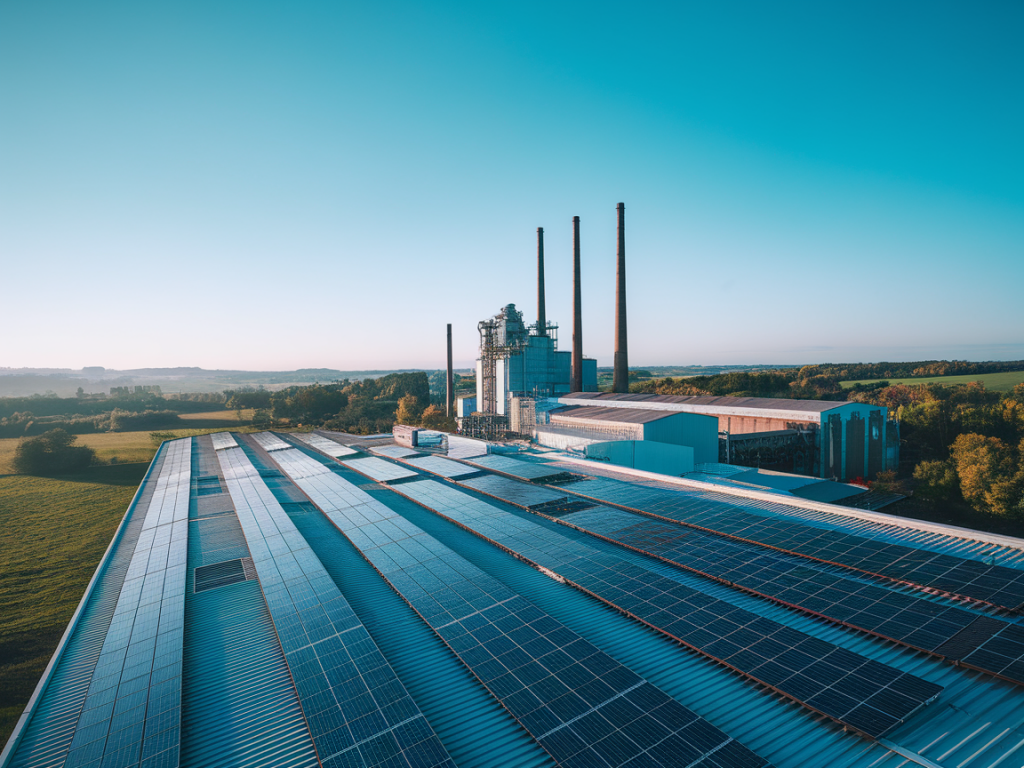
Depuis quelques années, une révolution discrète mais puissante est en cours dans le monde de l'industrie : celle de l’énergie. Les usines autonomes et plus vertes ne relèvent plus du fantasme ou de promesses lointaines ; elles deviennent une réalité tangible grâce à des innovations technologiques de pointe. Alors que les enjeux environnementaux se font de plus en plus pressants, nombreux sont les acteurs industriels qui expérimentent ou adoptent de nouvelles solutions énergétiques pour réduire leur empreinte carbone, améliorer leur efficacité et avancer vers une autonomie énergétique. Si vous êtes aussi fascinés que moi par ces transformations, plongeons ensemble dans cet univers passionnant !
Des micro-grilles pour une production décentralisée et flexible
Un des grands défis pour rendre les usines plus autonomes et respectueuses de l’environnement réside dans leur capacité à générer leur propre énergie. C’est là qu’interviennent les micro-grids, ou micro-réseaux électriques. Ces systèmes permettent à une usine de produire, stocker et utiliser sa propre électricité, voire de partager l’énergie excédentaire avec d’autres entités locales dans une logique collaborative.
Concrètement, ces réseaux décentralisés tirent souvent parti des énergies renouvelables comme les panneaux solaires installés en toiture, les petites éoliennes ou encore des systèmes de récupération d’énergie thermique. Prenons l’exemple des usines Tesla, qui déploient des systèmes de batteries géantes (les fameuses Powerpacks) combinées à des installations photovoltaïques pour alimenter leurs sites. L’objectif ? Une indépendance vis-à-vis des infrastructures énergétiques traditionnelles tout en démontrant la viabilité de ces technologies à grande échelle.
Mais tout n’est pas simple : stocker l’énergie intermittente produite par le soleil ou le vent reste un défi coûteux. Heureusement, les avancées dans les batteries au lithium, les supercondensateurs ou encore les technologies de stockage à hydrogène ouvrent des perspectives immenses.
Le recours à l’hydrogène : l’énergie propre au service des usines
Quand on parle d’autonomie énergétique et de transition verte, l’hydrogène occupe une place de choix. Cet élément, le plus abondant de l’univers, est en passe de devenir un acteur clé dans les chaînes industrielles. L’hydrogène "vert", produit à partir d’énergies renouvelables, permet non seulement de diminuer les émissions de CO2 mais également d’alimenter des usines avec une énergie propre, transportable et facilement stockable.
De nombreux géants industriels misent sur cette technologie. Air Liquide, l’un des leaders mondiaux de la production d’hydrogène, travaille sur des solutions adaptées aux besoins des usines. Aujourd’hui, certaines entreprises utilisent déjà des piles à hydrogène pour alimenter leurs engins ou même des processus internes comme le chauffage ou la climatisation. Imaginez des usines entièrement fonctionnelles, dont les émissions se résumeraient à de simples particules d’eau !
Certes, construire une telle infrastructure a un coût, mais les investissements des gouvernements et des entreprises sur cette énergie de rupture laissent entrevoir une adoption massive d’ici les prochaines décennies.
L’intelligence artificielle au service de l’efficacité énergétique
Optimiser la consommation d’énergie d’une usine est une autre clé pour réduire son bilan carbone, et l’intelligence artificielle (IA) s’avère être un outil particulièrement précieux dans cette démarche. Grâce aux systèmes d’apprentissage automatique, les outils de gestion énergétique deviennent capables d’analyser des milliers de données en temps réel pour ajuster les équipements, réduire les gaspillages et prévoir les besoins futurs en énergie.
Siemens, par exemple, propose sa plateforme MindSphere, capable d’agréger des données issues de capteurs connectés pour piloter la distribution énergétique de façon intelligente. Ce type de solution peut détecter des anomalies, prédire les périodes de forte demande ou même déclencher un basculement temporaire vers des sources énergétiques alternatives en cas de surcharge du réseau classique.
En utilisant des systèmes basés sur ces technologies, certaines usines ont réussi à réduire leur consommation d'énergie de près de 30 %. Et ce n'est qu'un début : l'IA combinée à la robotique pourrait bientôt permettre des cycles de production entièrement optimisés en termes de consommation énergétique.
L’économie circulaire : un levier pour des usines plus responsables
Une usine autonome et verte ne dépend pas uniquement des nouvelles sources d’énergie ; elle doit également adopter des modèles de fonctionnement qui limitent les déchets et maximisent la réutilisation des ressources. C’est ici que l’économie circulaire entre en jeu. Elle encourage les industriels à repenser le cycle de vie des produits et à exploiter les sous-produits d’un processus comme ressource pour un autre.
Par exemple, certains sites industriels utilisent la chaleur inutile générée par leurs machines pour chauffer les bureaux ou les logements voisins. D’autres transforment leurs déchets en biomasse qui peut ensuite être brûlée pour produire de l’électricité. Le groupe Veolia illustre bien cette tendance, en proposant des solutions de valorisation des déchets industriels pour générer de l'énergie à bas coût et réduire ainsi la dépendance aux énergies fossiles.
Ce modèle d’économie circulaire, encore balbutiant dans certains secteurs, promet de transformer le paysage de nombreuses industries dans les années à venir.
Les usines connectées et l'industrie 4.0
En parallèle de ces innovations énergétiques, l’idée des usines connectées prend de plus en plus d’importance. Ces "smart factories", résultats de la convergence entre l’IoT (Internet des Objets), le Big Data et l’automatisation, intègrent des solutions qui ne se contentent pas de produire de l’énergie propre, mais adaptent également en temps réel leurs processus pour minimiser leur impact environnemental.
Prenons le cas de Schneider Electric, qui a fait de nombreuses de ses usines des modèles d’usines connectées. Ces sites, intégralement automatisés et numérisés, optimisent chaque étape de la production en collectant des données grâce à des capteurs. Les applications logicielles ajustent ensuite l'éclairage, la climatisation ou le fonctionnement des machines selon les besoins exacts, éliminant ainsi les gaspillages énergétiques. Impressionnant, non ?